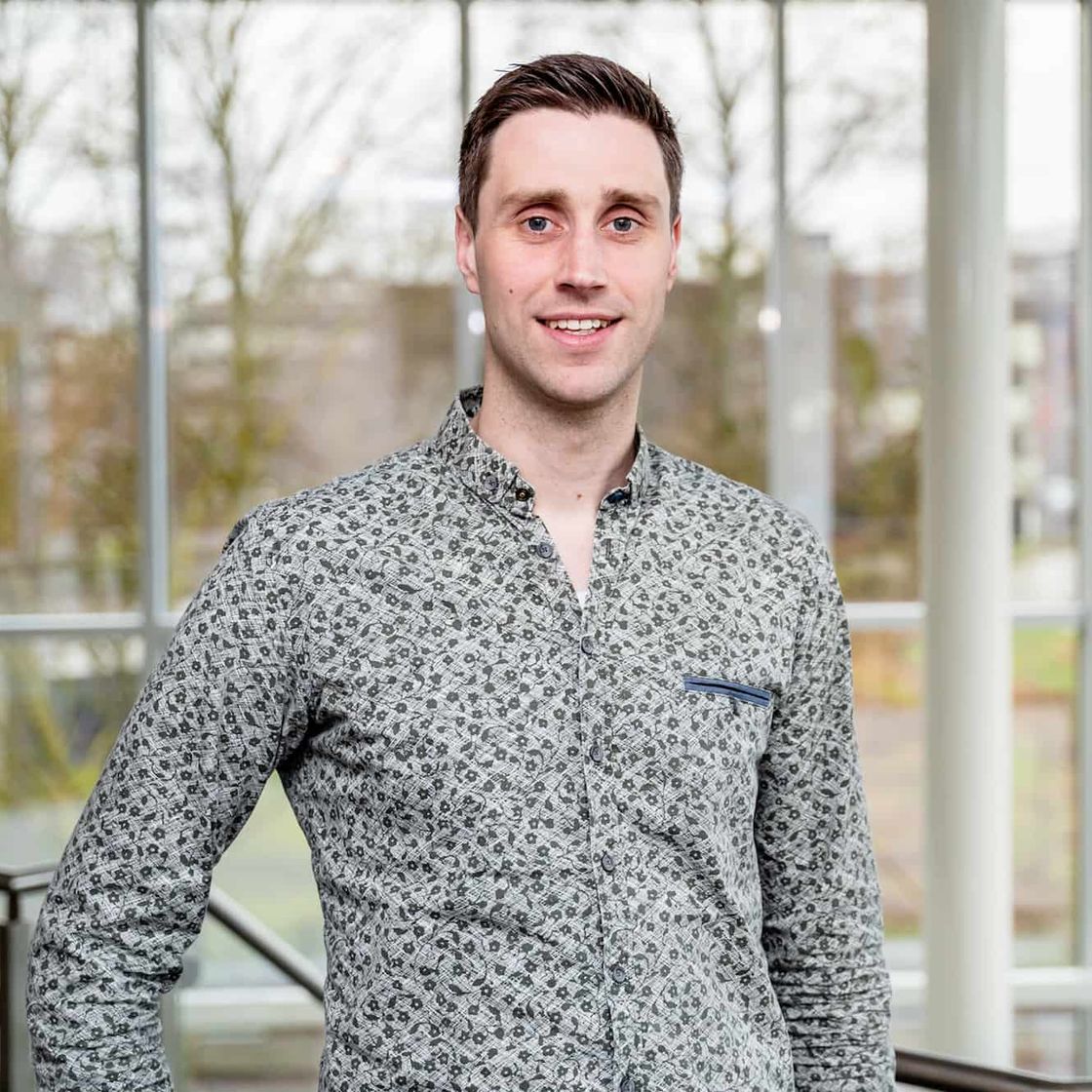
high volumes, high precision.
Military personnel are using more and more electronic devices for operations and communication in the field. The E-Lighter has been developed to replace the many spare batteries. It works with many thermoelectric elements that convert energy from diesel into electricity. These pellets are produced from pressed metal powder and then milled to size. Due to the high volumes, the required high precision and the classification of the metal powder as a hazardous substance, a (semi) manual solution was not feasible. We developed a fully automatic and safe solution and provided it with adequate quality control.
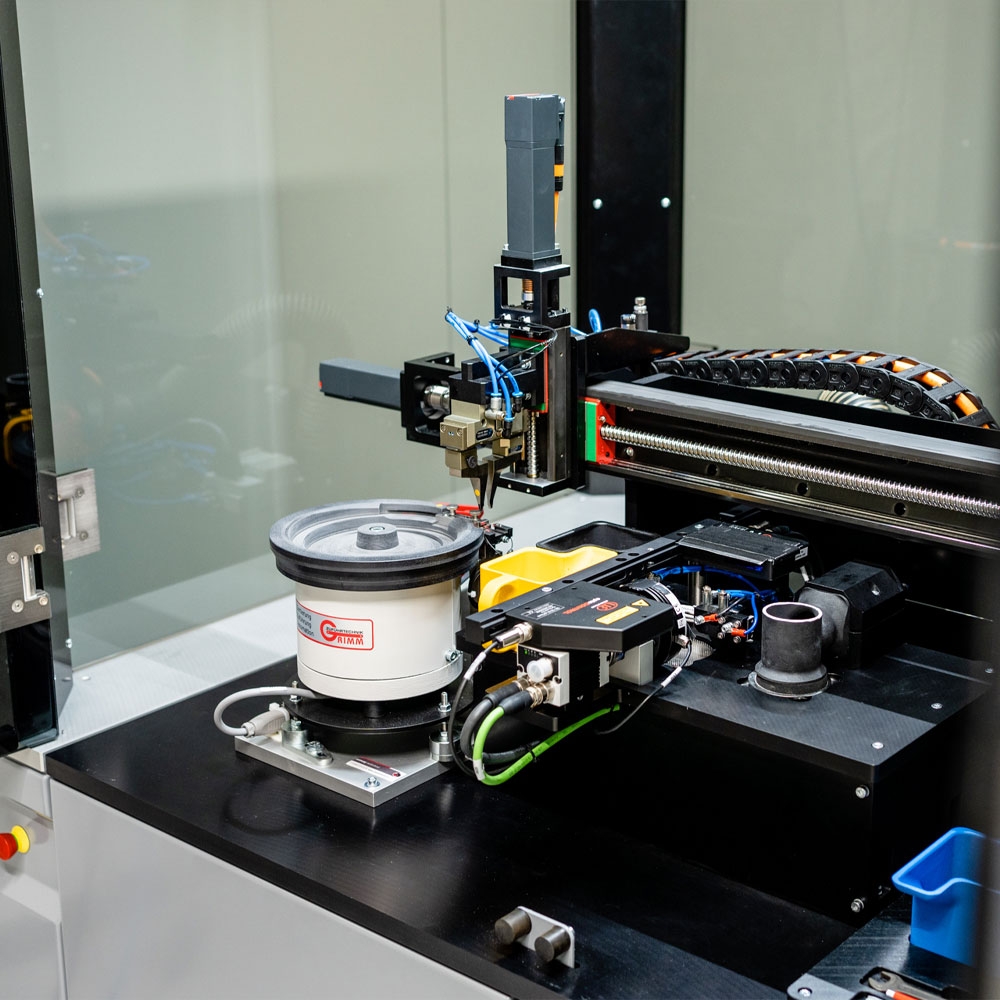
highlights
- Smart Machine Base standard platform
- safe and dust-free system
- precise milling and length measurement
- [+0.05, –0] mm tolerance
- integrity control using electrical resistance measurement
measuring, milling and measuring.
A critical function proved to be infeed of the pressed pellets, which are small and fragile. We developed a solution with a vibratory filler. At the exit, the randomly oriented pellets are picked up using two servo-controlled screw spindles and a pneumatic gripper. Due to the specified tolerance, the length of each pellet is accurately measured before and after milling. We also looked at damage, such as cracks, as a result of the processing. To ensure the internal integrity of the pellets, we added an electrical resistance measurement. Rejected pellets are automatically sorted out. Naturally, dust is extracted during milling; for this we installed a system with HEPA filters.
“we found the right settings for good performance.”
We built the complete milling machine on our standard SmartMachineBase platform. As a result, we were able to focus on the specific technical challenges during the short lead time of the project. For example, we found the right settings for many parameters during the test phase, enabling us to guarantee good performance.
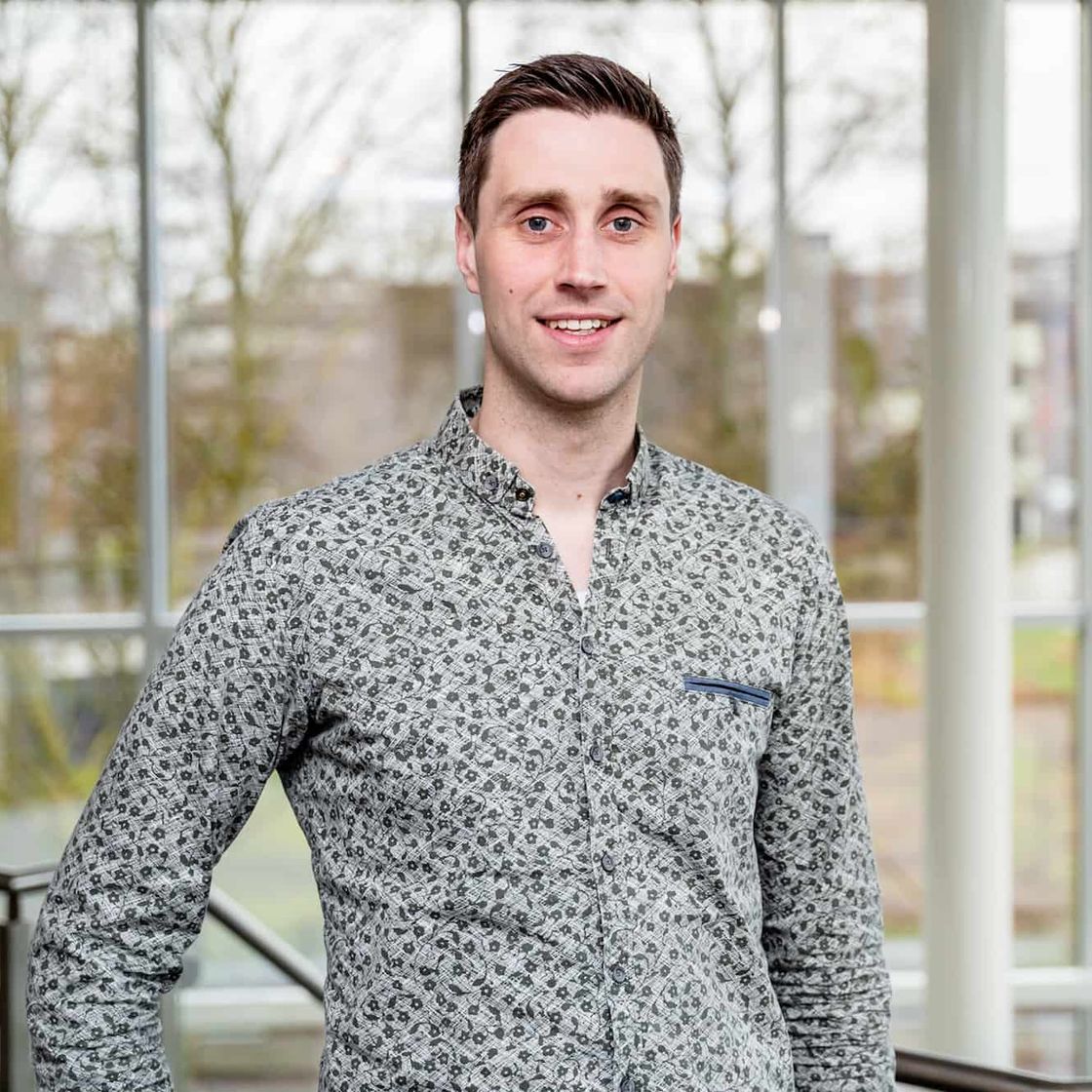