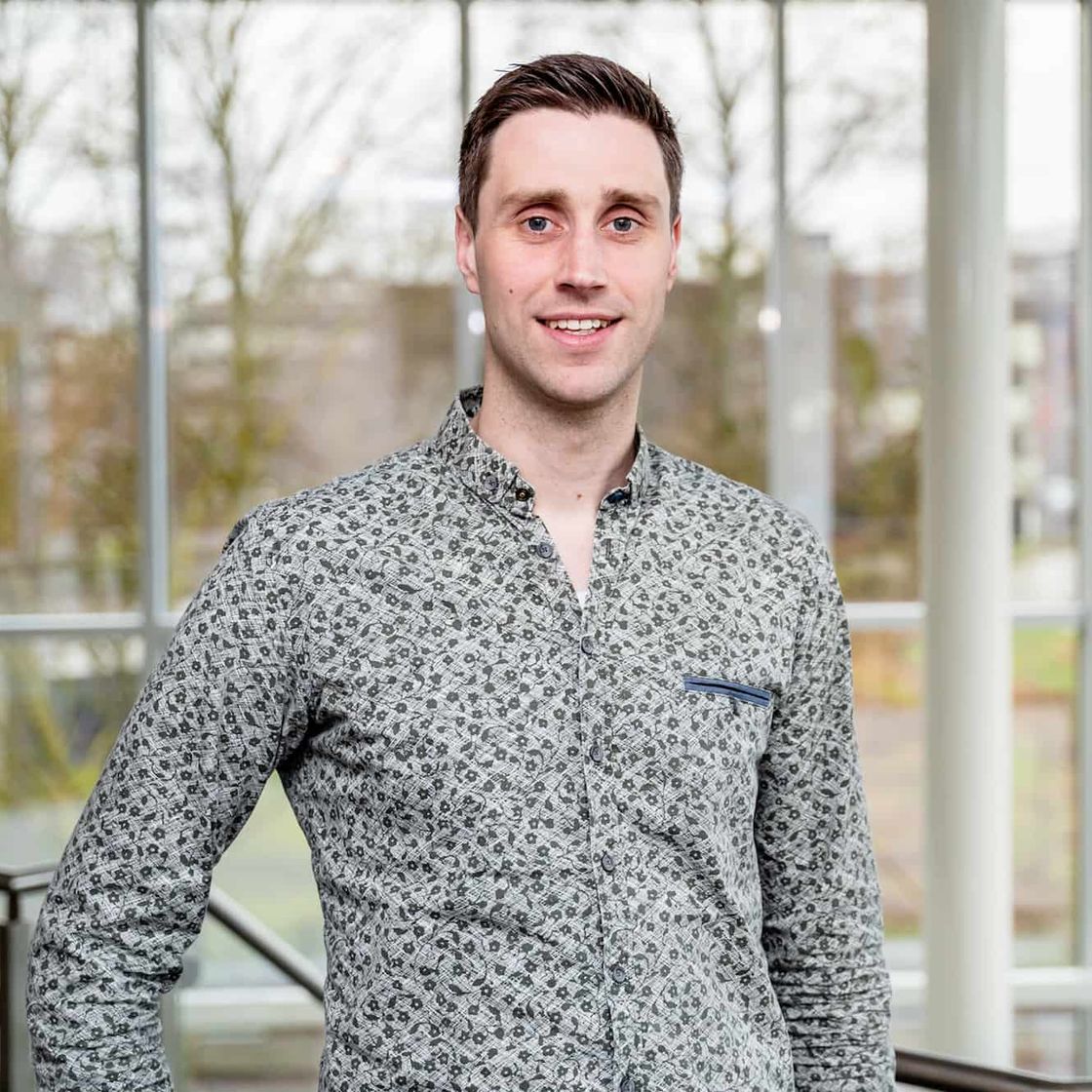
broad expertise.
Cutting film and laminating it onto photosensitive material proved to be a critical step in the production process for the new film cartridges. For this purpose, we developed a new cutting and laminating module. It needed to fit in with the old line, be prepared for new technologies and comply with current safety guidelines. We used our expertise in system architecture, mechatronics, system integration and industrialization to realize a reliable working module. After a thorough system analysis, we evaluated concepts for the main functions of cutting, laminating and foil guiding and converted these into a system concept. Criteria were proven technology, easy testability and reliability.
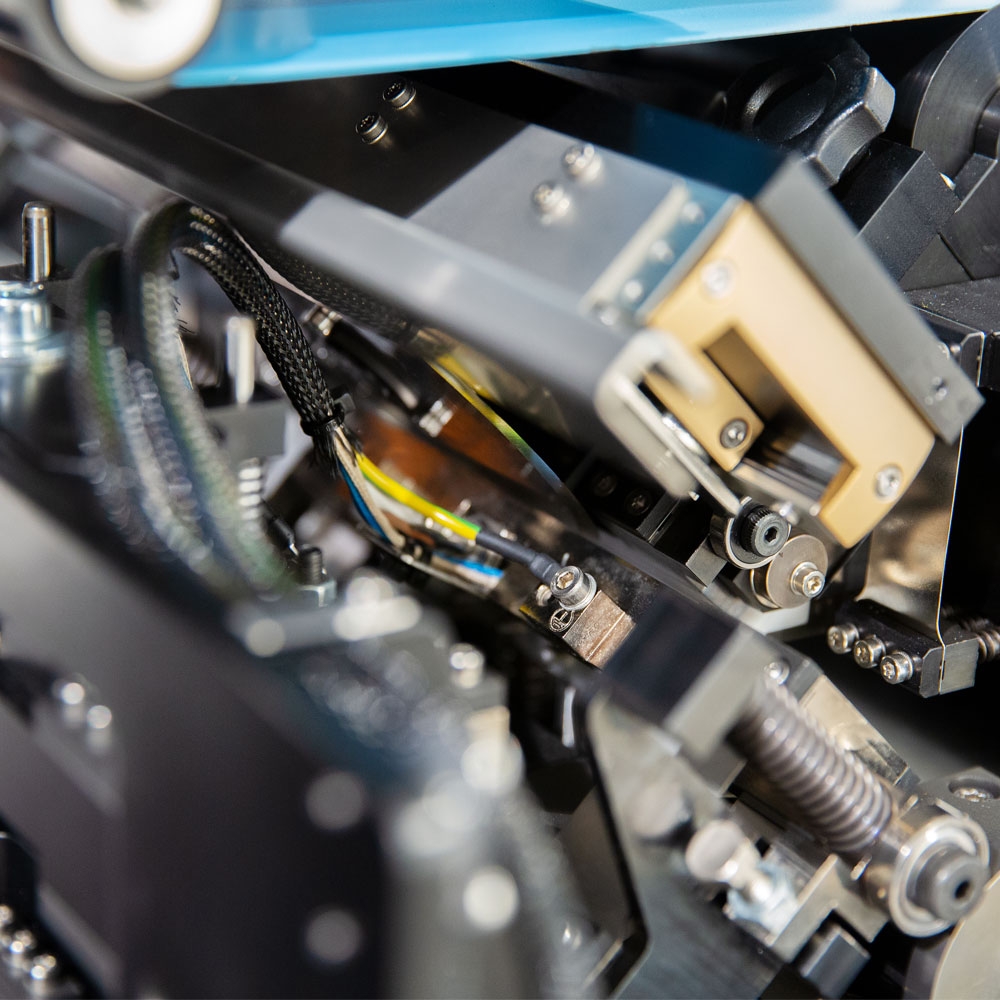
highlights
- reliable, low-maintenance module
- high production speed
- long lifetime
- higher OEE of production line
robust solution.
The best option for cutting turned out to be a circular knife: good cutting quality, long tool life and easy tool exchange. For lamination, the choice fell on the well-known “hot blocks”, now with the application of modern materials, among other things for better heat transfer. Guiding the material was possible with the existing technique, in which the web (the foil) is pulled through the module under tension and clamped during processing.
An encoder on the main shaft enables exact timing of the various process steps. The use of leaf springs and rotating techniques (bearings) ensures a long service life. The new module can run at high speed (for approximately 180 films per minute) and process different materials, has a long lifetime and is maintenance-free as much as possible. In this way, we helped increase the OEE (operational equipment effectiveness) of the complete production line at Polaroid.
“we realized the ‘impossible’.”
Retrofit is often difficult due to limited volume budget, existing interfaces and the introduction of new production techniques. This also applied to Polaroid, which did not restart under the name “Impossible Project” for nothing. Thanks to the use of our broad expertise, the “impossible” turned out to be possible after all. After our concept study, we delivered a working module within a year.
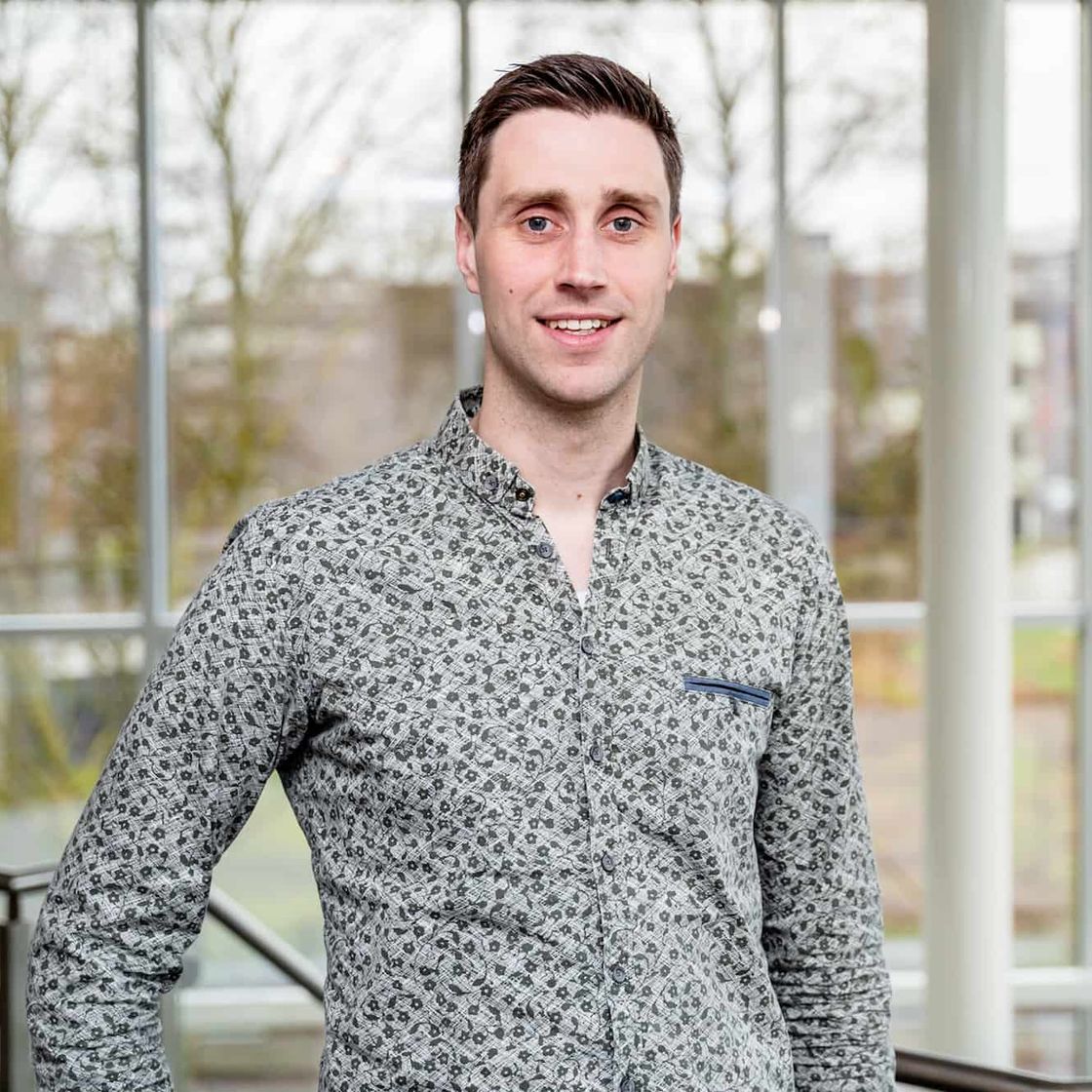